Selective Laser Sintering (SLS)
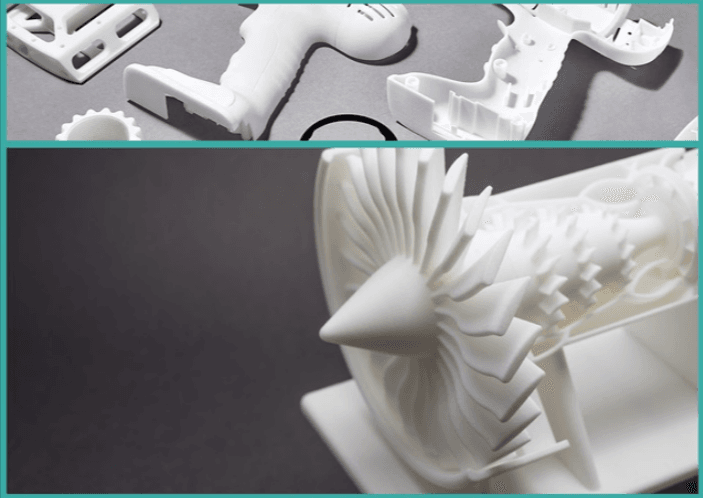
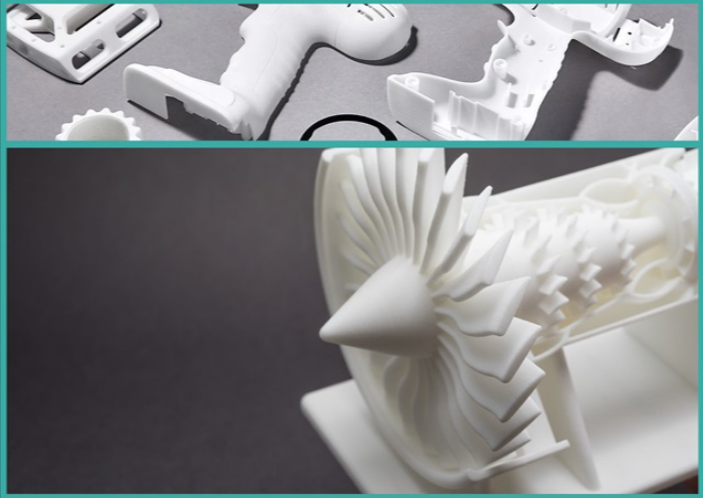
Unlocking Accuracy
Selective Laser Sintering (SLS), a member of the Powder Bed Fusion family, is a leading industrial 3D printing process. By precisely sintering polymer powder particles layer by layer using a laser, SLS technology brings CAD designs to life, making it a preferred choice for both end-use part manufacturing and prototyping.
USP
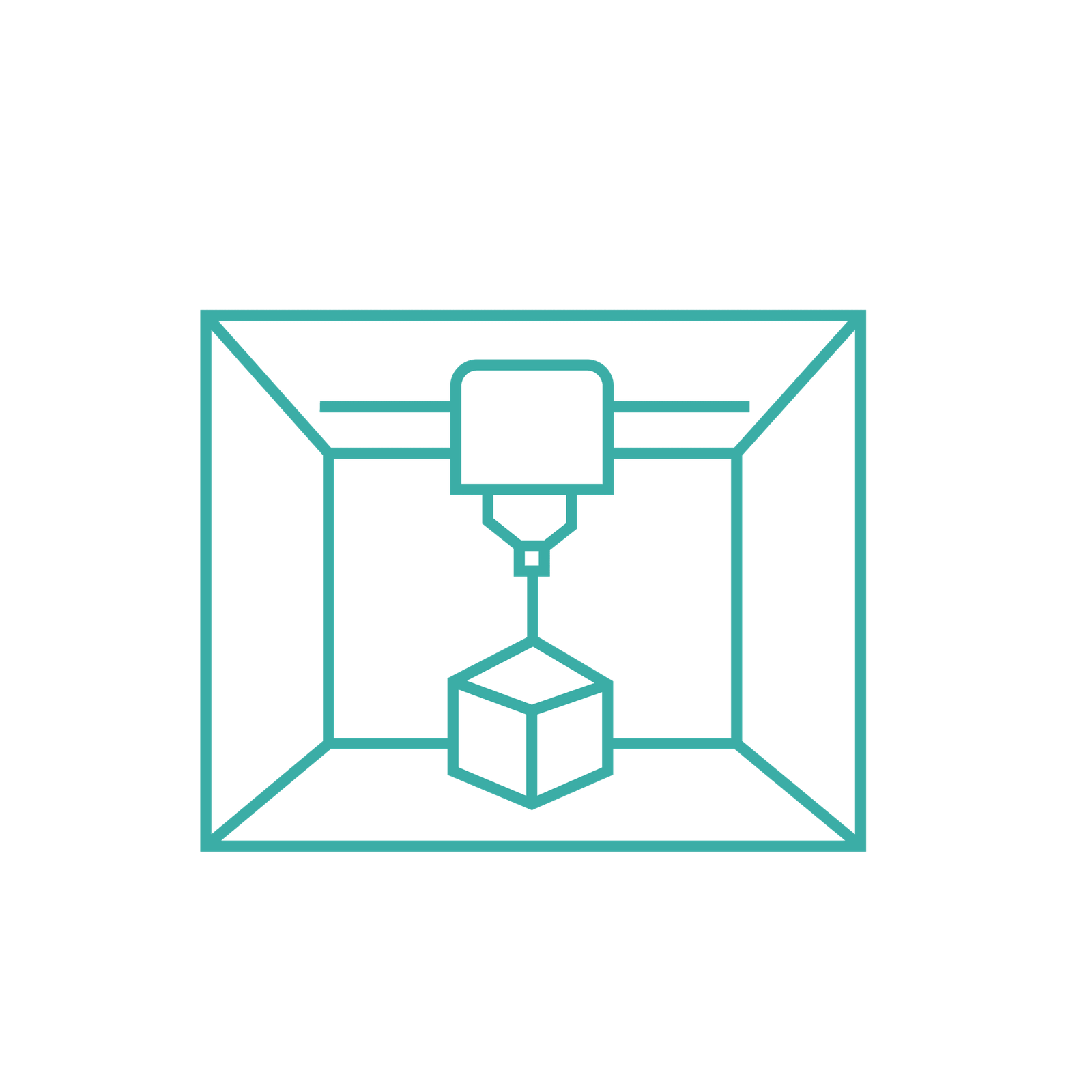
Support-Free Printing
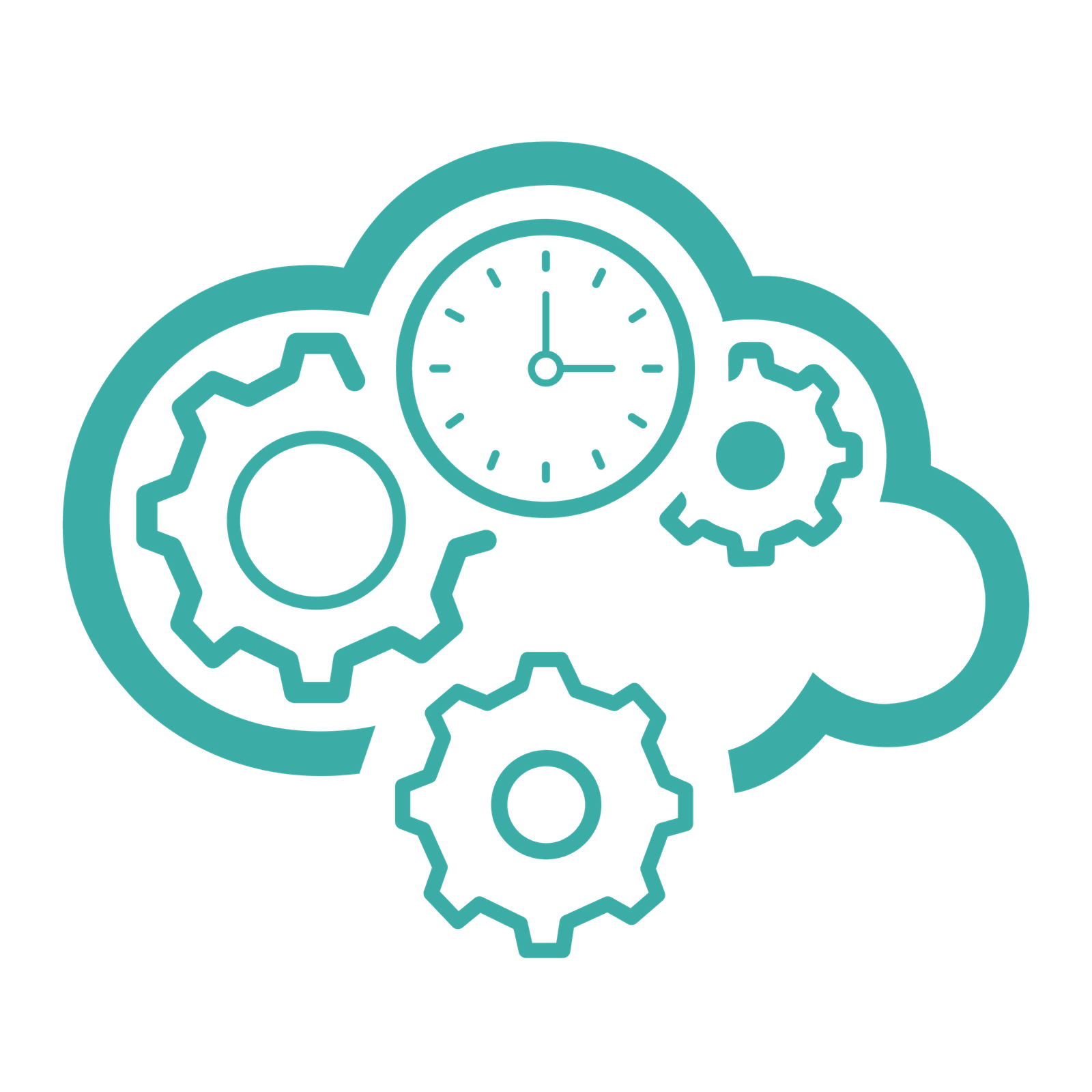
Minimal Post Processing
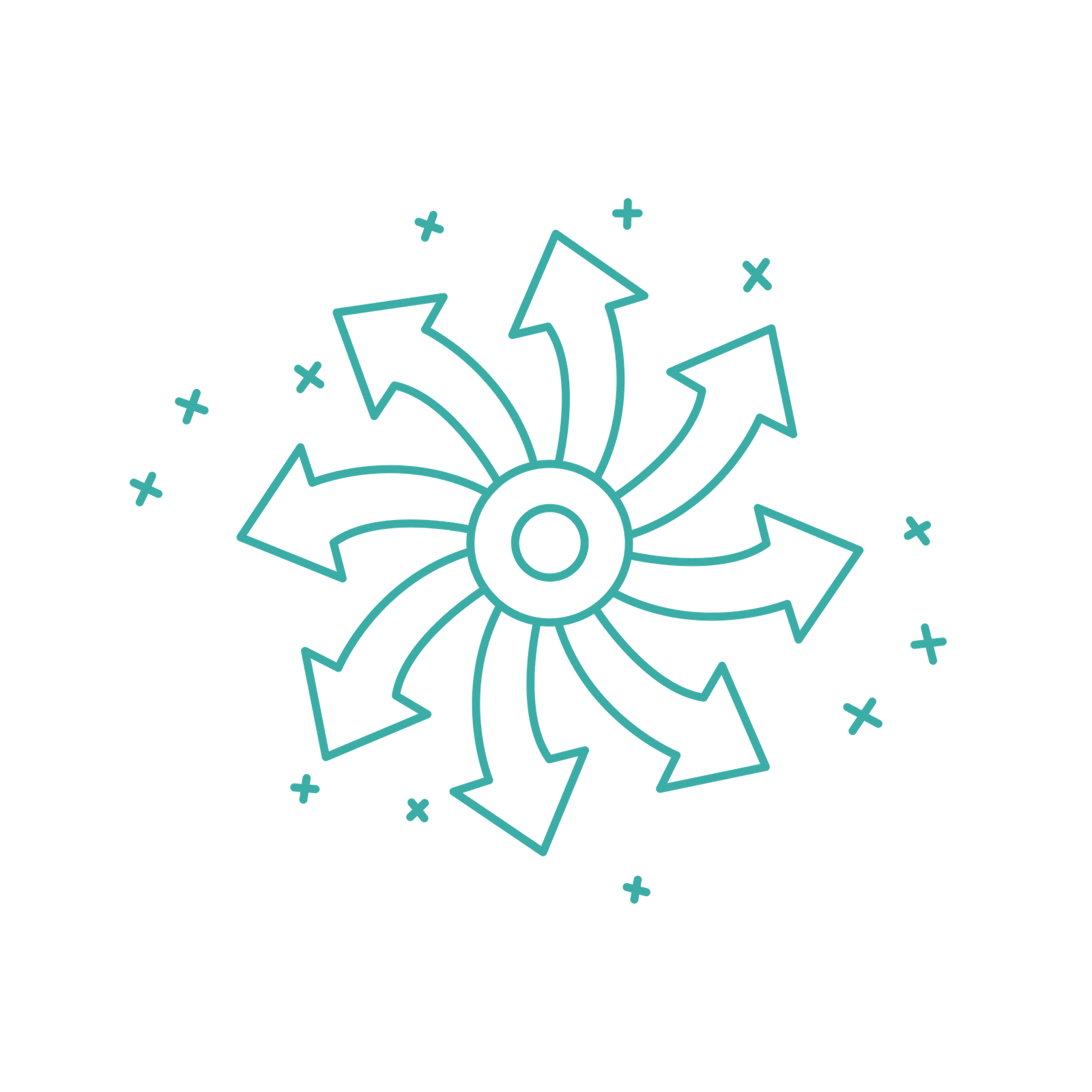
Versatile Geometries
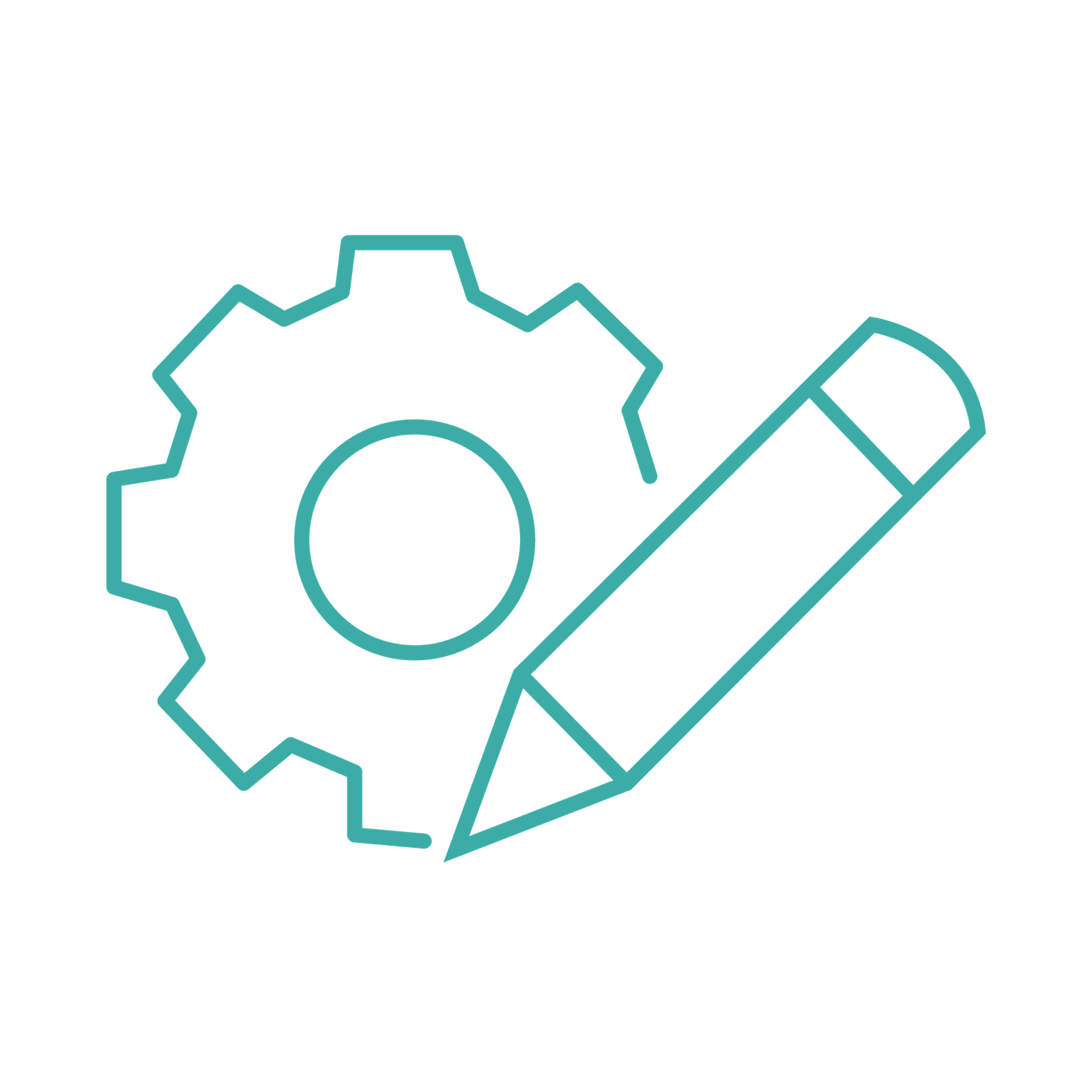
Customisation
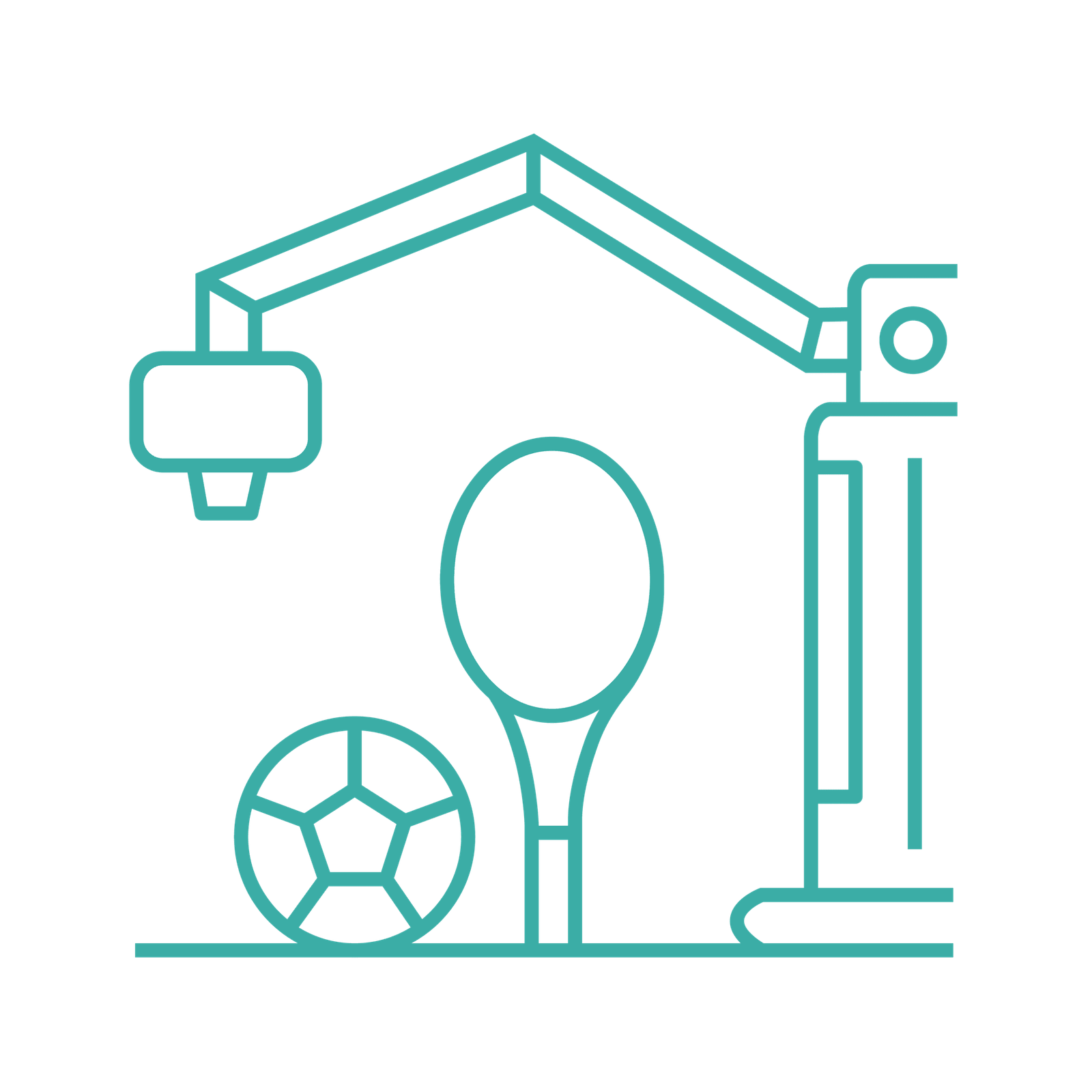
Functional Prototypes
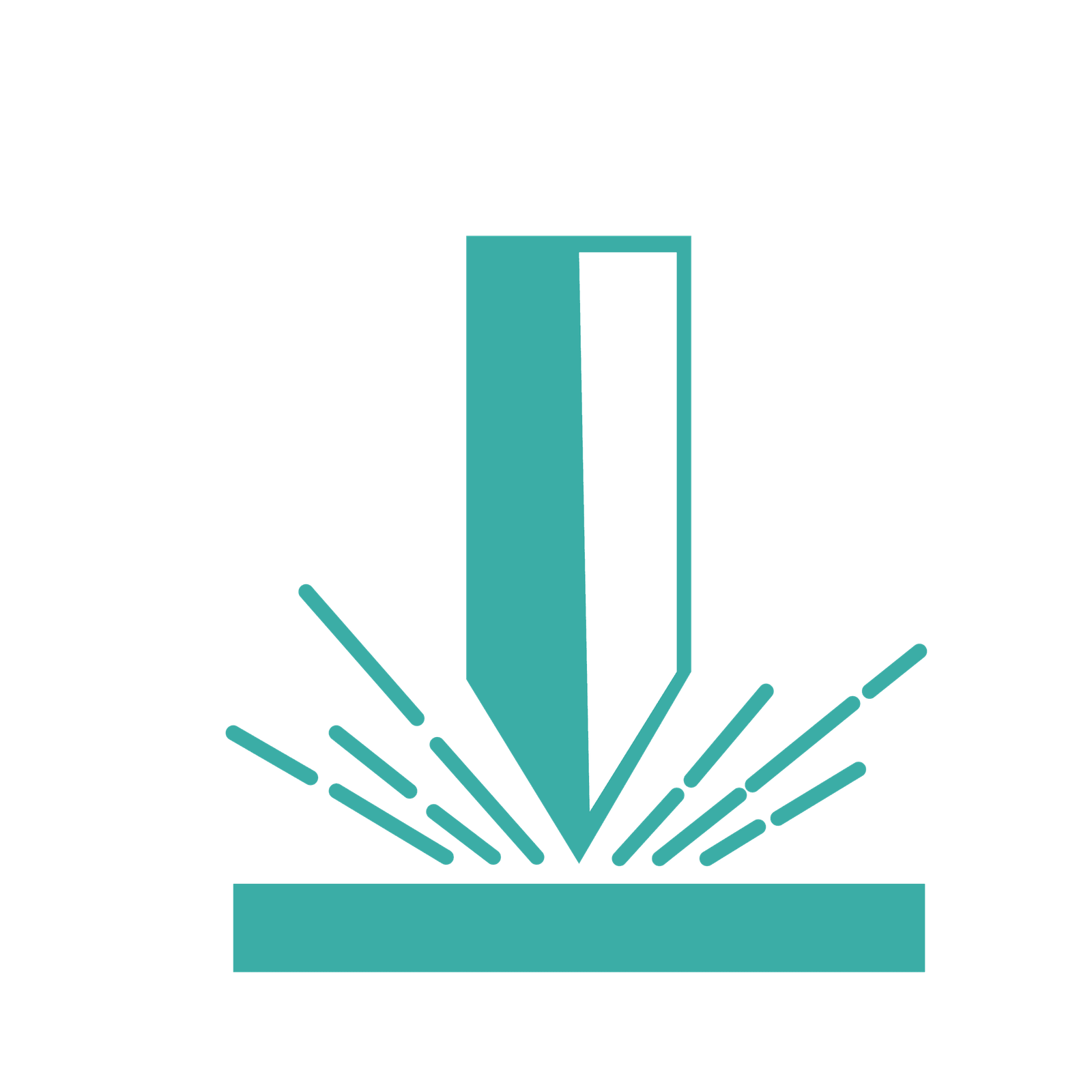
Impact Resistance
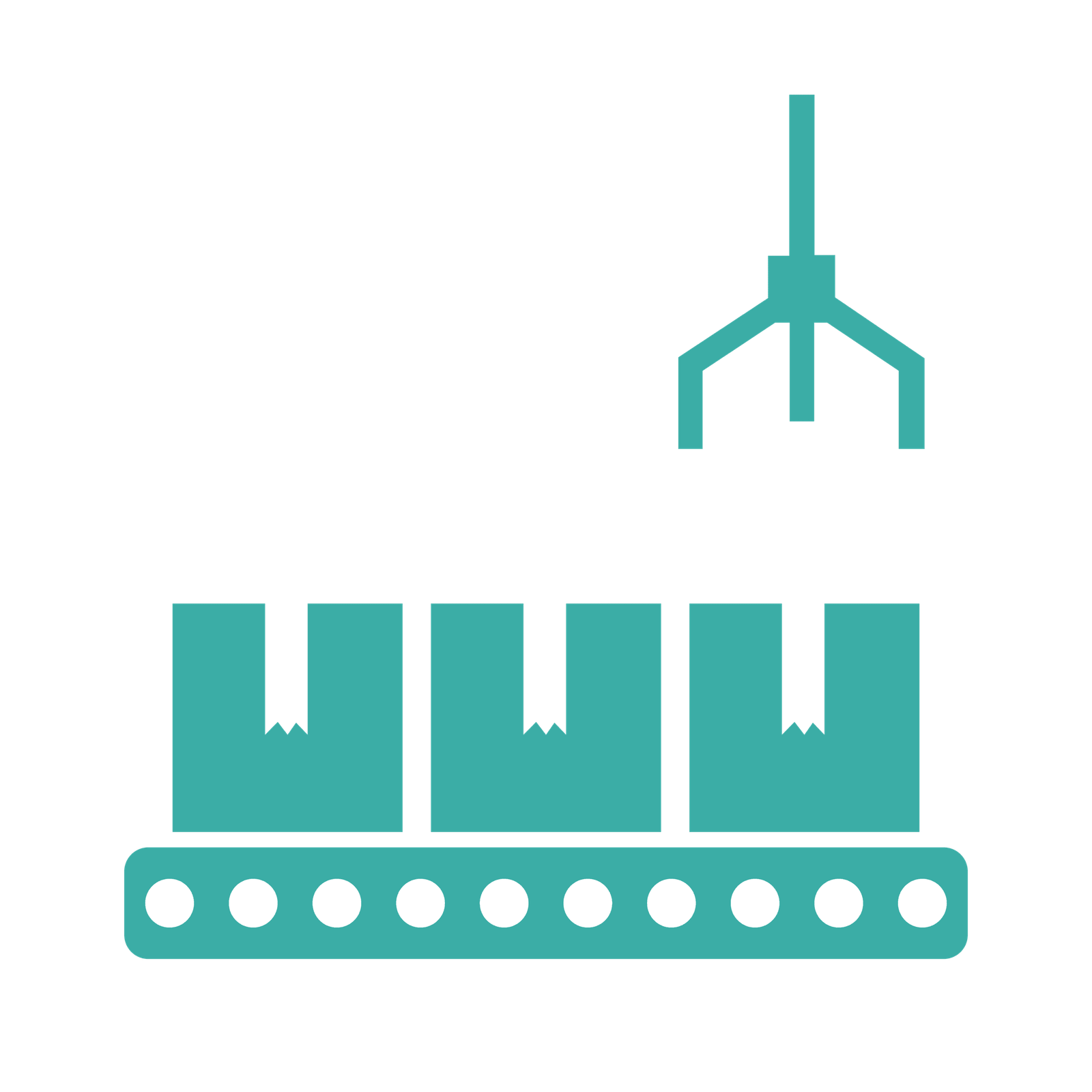
Low Volume Production
Our Post Processing Offerings
Our Material Offerings
Industries
Why Choose Tesseract for Selective Laser Sintering (SLS)?
Tesseract stands at the forefront of 3D printing innovation, and our expertise in Selective Laser Sintering (SLS) is a testament to our commitment to quality and precision. SLS is an advanced additive manufacturing process that uses a high-powered laser to fuse small particles of polymer powder into solid structures. This technique is ideal for creating robust, functional prototypes and end-use parts with complex geometries. Choosing Tesseract for your SLS needs ensures you benefit from cutting-edge technology and exceptional service.
Applications & Use Cases
SUPPORT-FREE PRINTING
SLS technology eliminates the need for support structures during the printing process. This feature allows for greater design freedom and the creation of intricate geometries that would be challenging with other 3D printing methods.
MINIMAL POST PROCESSING
With SLS, the printed parts require minimal post-processing. The absence of support structures reduces the need for manual removal, sanding, or other finishing steps, saving you time and effort.
VERSATILE GEOMETRIES
Our SLS capabilities can handle a wide range of geometries, from simple shapes to highly complex structures. This versatility makes it suitable for various applications, including aerospace components, medical devices, and automotive parts.
CUSTOMISATION
SLS technology allows for high levels of customization. Whether you need small batch production or tailored prototypes, we can adjust our processes to meet your specific requirements, ensuring each part is perfect for its intended use.
FUNCTIONAL PROTOTYPES
The strength and durability of SLS-printed parts make them ideal for functional prototypes. These parts can withstand rigorous testing and real-world conditions, providing valuable insights into the performance of your designs.
IMPACT RESISTANCE
SLS parts are known for their excellent impact resistance. This property is crucial for applications that require durable and resilient components, ensuring your parts can endure demanding environments and stresses.
LOW VOLUME PRODUCTION
Tesseract offers cost-effective low volume production with SLS. This capability is perfect for producing small quantities of parts without the high costs and long lead times associated with traditional manufacturing methods.
Choosing Tesseract for your Selective Laser Sintering needs means opting for precision, innovation, and reliability. Our dedication to excellence ensures that every project, regardless of its complexity or scale, receives the highest level of attention and care. Trust Tesseract to transform your ideas into reality with our state-of-the-art SLS technology, delivering parts that meet and exceed your expectations.