Automotive
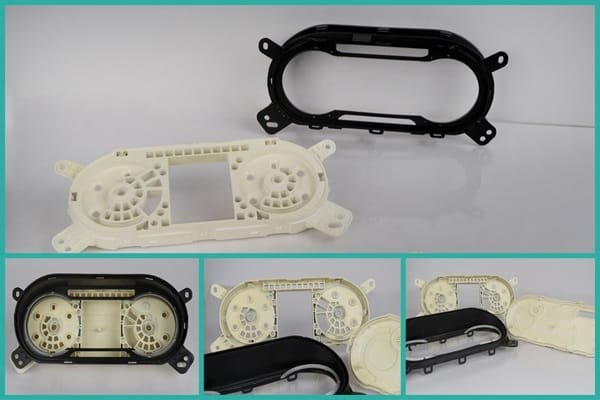
Revolutionising the Automotive Industry with 3D Printing
Recent advancements in Additive Manufacturing (commonly known as 3D printing) have unleashed a new era of innovation in the automotive sector. With the freedom to explore robust designs and benefit from lighter, stronger, and safer products, the automotive industry is embracing 3D printing for enhanced efficiency and cost-effectiveness. From swift prototyping of physical parts to envisioning an entire car through scale models, 3D printing empowers designers to transform ideas into convincing proof of concept, paving the way to high-fidelity prototypes mirroring the end result.
Applications
- Body & Exterior Components: Rapid fabrication of body parts and exterior components with improved designs and reduced lead times.
- Obsolete and Discontinued Spare Parts: On-demand production of spare components, addressing challenges posed by unpredictable demand for previously discontinued spare parts.
- Interior Components: Crafting intricate interior elements and dashboards with precision, optimising design and functionality.
- Jigs, Fixtures and Brackets: Customised manufacturing aids improved assembly processes, enhancing efficiency and safety on the factory floor.
- Prototypes: Efficient prototyping of automotive parts and assemblies for swift design iterations and improvements.
- EV Components: Production of specialised components for electric vehicles, utilising materials with high-temperature resistance, a crucial aspect of EV applications.
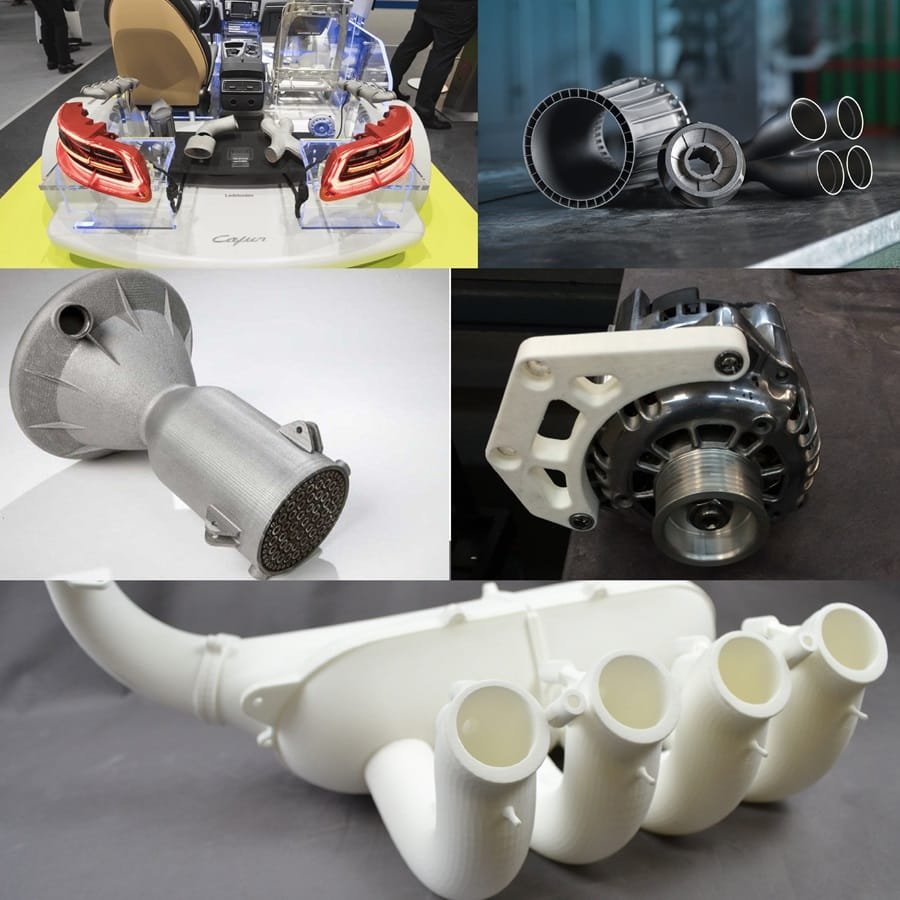